図面が出来上がったら、製作・工事に入る前に「検図」を行います。
会社によっては図面チェック、図面確認、図面承認、と呼び方は様々ですが、
「図面にミスや問題が無いか確認する作業」の事を言います。
エンジニアリングを進める上で検図は非常に大切な作業ですが、
経験が少ないうちは膨大な図面のどこを見て良いか分からず、
時間を浪費してしまいます。
本記事では設備設計の初心者に向けて、
検図において確認すべきポイントをまとめました。
設備設計における検図の重要性
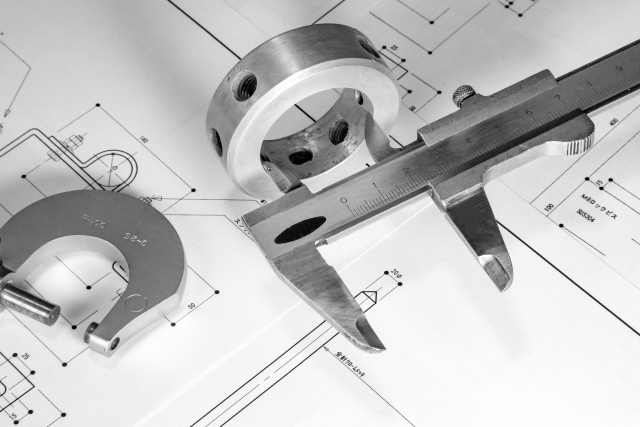
製造業におけるトラブルの9割は設計が原因だと言われています。
特にプラント業界の設備設計では、万が一設計に問題があると、
その後の製作・組立・工事・メンテナンス・安全の全てに悪影響が出てしまいます。
こうした問題を事前に防ぐのが設計者の役割であり、
その最後の砦となる重要な作業が、「検図」になります。
検図において大切な考え方:「かすり傷は負っても致命傷は負うな」
設備の規模にもよりますが、検図を行う際には数十枚、
場合によっては100枚以上もの図面をチェックする必要があります。
こんな枚数の図面を担当者1,2人で全て細かくチェックしていては、
何時間あっても検図は終わりません。
そこで検図において大事な考え方が、
「かすり傷は負っても致命傷は負うな」というものです。
致命傷となる大きなミスを防ぐことを最優先とし、
かすり傷程度の小さなミスは万が一発生しても許容する、という考え方です。
要するに「重要な部分にだけポイントを絞って検図する」という事です。
この検図において重要なポイント(=チェック漏れすると致命傷になる部分)が何か?
という感覚は経験によって培われる物で、慣れの部分が大きいと思います。
以下に検図で確認すべきポイントををまとめますので、参考にしてください。
検図で確認すべきポイント
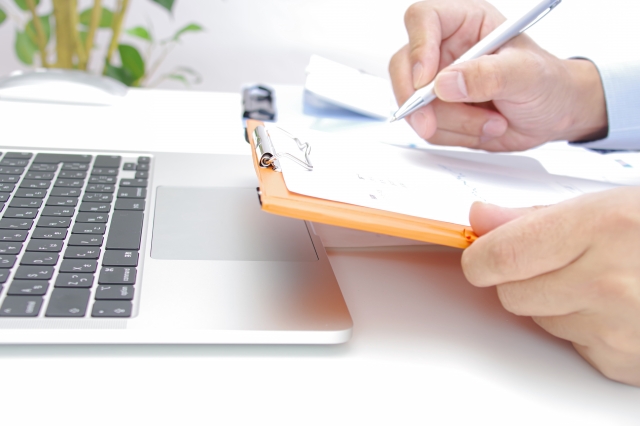
検図を行う際は、致命傷となる大きなミスを防ぐことが先決です。
設備設計での致命傷とは、大きく以下の6つに分ける事ができます。
- 設備の主仕様を満たしていない
- 部品の組立、製作ができない
- 設備を予定の位置に据え付けられない
- 設置後すぐに故障してしまう
- 設置後のメンテナンスができない
- 安全性に問題がある
これらに一つでも当てはまってしまうと、
せっかく作った設備が「使えない設備」となってしまいます。
逆に言えば上記の6つの致命傷を避けられている事を確認できれば、合格点です。
順番に解説します。
設備の主仕様を満たしているか
主仕様に認識違いは無いか
図面に記載された仕様が、生産部門や顧客から要求された仕様の通りか、確認しましょう。
図番の最初にくる全体組立図に、主仕様を表にして記載する事が多いです。
設計の大前提となるこの部分に誤認識があれば以降の設計は全て無意味になります。
主仕様を満たせる機器構成になっているか
図面通りの機器構成で主仕様を満たせるか確認します。
どんな設備かによって検図するポイントは異なりますが、
以下を重点的に確認するとよいです。
- 流体を扱う設備:流量、圧力、配管径、圧損、ポンプ容量、バルブの種類と位置
- 可動する物がある設備:モーター容量、回転数、可動範囲、シリンダストローク量
- その他全般の設備:材質、温度、センサー個数
部品の組立、製作が可能か
組立手順はイメージできるか
部品は取込口から目的地まで干渉なく入っていけるか、
物理的に組立できる構造になっているか、確認しましょう。
例えば、長い軸の途中にリング状の部品をはめたい時は、
軸径よりもリングの径の方が大きくないと通っていきません。
設備が複雑になってくると意外と見落としがちです。
自分で組立手順をイメージしながら検図するとよいです。
ボルト・ナットに手が届くか、工具で回せるか
ボルト・ナットが他の部材で隠れていたり、
工具で回せないような狭い位置にあると、ボルト固定できません。
一つの設備にボルト・ナットは大量に使われているので確認が大変ですが、
「奥まった場所」や「ごちゃごちゃしてる場所」などポイントを絞って確認するとよいです。
溶接部に手が届くか、溶接時に無理な体勢にならないか
上記のボルト・ナットの確認と似ています。
ただ溶接の場合は、「施工者が溶接する時の体勢」が溶接品質に効いてきます。
無理な態勢での溶接・手が届くか微妙な距離での溶接は、
溶接品質が悪くなり、強度が不足して破断の原因になります。
溶接してくれる施工者の気持ちになって、どの体勢で溶接する事になるか?
をイメージしましょう。
設備を予定の位置に据え付けられるか
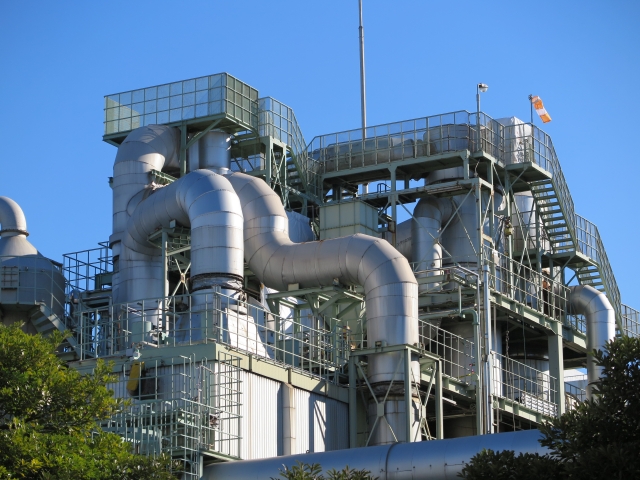
既設範囲と新設範囲の取合いは明記されているか
既設範囲と新設範囲の境目となる位置を「取合い」と言います。
この「取合い」が明記されているか、しっかり確認しましょう。
これを怠ると、準備する部材・機器に過不足が生じたり、
施工者が施工範囲を勘違いして、現場を混乱させます。
既設側の位置が予想と少しずれていた場合、調整代はあるか
前項目の「取合い」を図面に書く際、
既設側の穴やボルト、配管フランジの位置を書くことになると思います。
これら既設側の情報は、既にある図面を調査したり、
現場で実寸法を測って書かれると思いますが、
どうしても数mm程度の誤差はあります。
この誤差が「全くのゼロ」の前提で物を製作して工事に臨むと、
現場でボルト穴が入らなかったり、据付レベルがずれたり、
配管が微妙に届かなかったりします。
これを防止するため、
「取合い」の位置には多少の誤差はある物だという前提で設計する事が重要です。
例としては、
- 取合い位置の穴径を、わざと少しだけ大きく設計する
- レベル調整用の薄い板(ライナーと呼びます)を用意する
- 一部の配管は現場溶接に変える
といった工夫をするとよいです。
周りの物と干渉しないか
新たに設置する機器が周りの物と干渉する場合、
当然ながら予定の位置には設置できないので、
事前に図面・現場で入念に確認しておく必要があります。
このとき、可動しない設備同士での干渉確認であれば楽ですが、
どちらかが可動する設備である場合は、特に注意が必要です。
シリンダーで動く設備であれば、シリンダーストロークの限界まで動かした時に干渉しないか、
図面に明記しましょう。
「この部材がここまで動くはずだが、それでも干渉しない」
とパッと見で分かるように書くとよいです。
設置後すぐに故障しないか
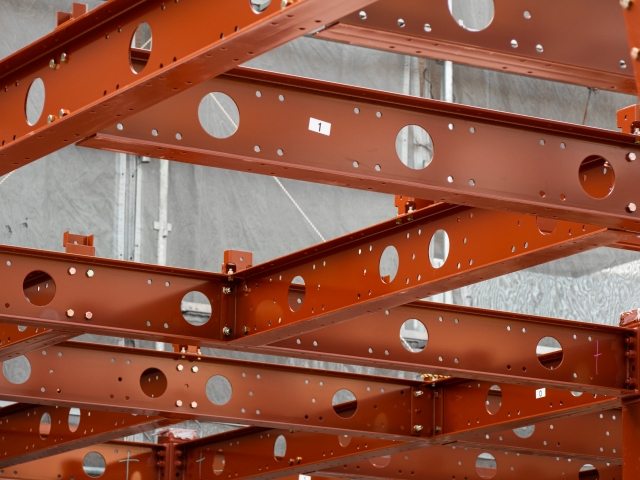
主要部材の強度は十分か
主要部材の強度が十分か確認しましょう。
駆動系などの特に重要な部材であれば、発生応力と許容応力を算出し、
ちゃんと強度計算した方が良いです。
検図の段階ではそれらの計算は終わっているはずなので、
計算結果をチェックするだけで済む事がほとんどです。
重要でない部材は、似た設備と比較して強度が下がる方向になっていないか?
だけを確認すれば、検図の時間を短縮できます。
自重や外荷重を受ける箇所の強度は十分か
XYZ方向の力をそれぞれどこで受けるか、
不自然に弱い箇所で受ける構造となっていないか、を確認します。
この時、「力の流れ」を意識するとよいです。
例えば机の上に物を置いた場合、
机の天板→机の脚→床という順番で力が伝わるはずですよね?
この順番の事を「力の流れ」と呼びます。
「力の流れ」の中に、一つでも強度の弱い部材があると、そこから壊れていきます。
こうした部材が無いかを確認しましょう。
設置後のメンテナンスが簡単か
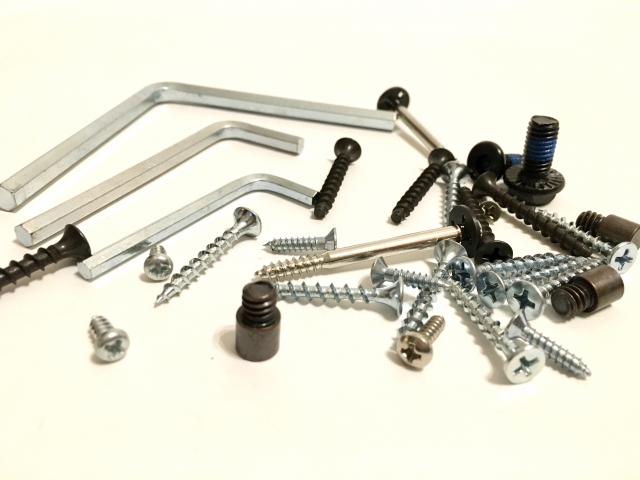
高頻度で交換する部品、消耗品が取外し難くなっていないか
検図においては、メンテナンス性など「設備を設置した後の事」も考えなくてはなりません。
損傷が激しく高頻度で交換する部品、ベアリング(軸受)やオイルシールなどの消耗品が、
取外し難い設計になっていないか確認しましょう。
消耗品一つを取り外すために、他の部品をいくつも解体する必要のある設備は、
良い設計とは言えません。
メンテナンス性の悪い設備は故障しても直し難くなり、やがて使われなくなります。
せっかく設計した設備を長く使ってもらえるよう、しっかり検図しましょう。
日常点検が必要な部品が見えない位置にいないか
破損したら一発で設備が止まるような重要な部品は、
交換のタイミングを見極めるために、日常的に点検すると思います。
その時に見えない・見づらい位置に部品があると、
適切な交換タイミングを見逃す恐れがあります。
壊れて設備が停止してから初めて気付く、
というパターンが最悪です。
交換タイミングを見逃さないためにも、
重要な部品は外から見やすい位置に配置する、点検窓を設けて点検し易くする、
などの工夫が必要です。
安全上の問題がないか
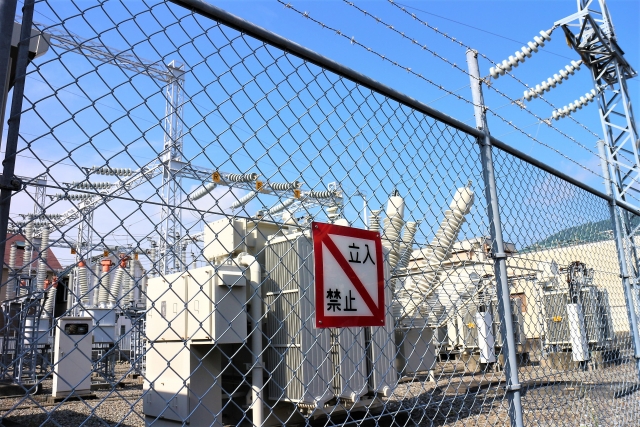
可動する物がある場合、身体が挟まれないか
設備のオペレーターや整備担当者に対する安全性も、設計者が担っていると言えます。
検図で安全性に関する確認が漏れ、災害が発生した場合、
設計者が責任を問われる可能性もあります。
安全性に関する部分はしっかり確認しましょう。
災害の中でも発生率・死亡率が高いのが、
「可動する物に対する身体の挟まれ」です。
可動範囲の限界まで物が動いた時に、
人の身体が挟まれない程度の隙間が設けられているか確認しましょう。
可動範囲を端から端まで図面に明記する事がポイントです。
回転体が露出しており、巻き込まれないか
軸、ギヤ、ロール、カップリングなどの回転体が露出している場合、
手指が巻き込まれる可能性があります。
回転体にはカバーを設置しましょう。
この時、単に覆ってしまうと点検がし難くなりメンテナンス性を損なうので、
点検窓付きのカバーにすると良いです。
高温物が露出しており、火傷しないか
温度は目に見えないため、高温物が露出していると、
うっかり触れて火傷を負う可能性があります。
高温物を扱う場合はどの範囲が高温となるか確認し、
人が触れないようにカバーを設置しましょう。
階段や通路の位置、手摺の高さは適切か
大きな設備を扱う場合、階段や通路、手摺も設置すると思います。
人が通る場所なので、可動する物・回転体・高温物が近くに無いか、
手摺が低くて墜落しないか、をしっかり確認しましょう。
また階段の各ステップの高さや通路幅も、通行し易さを左右しますので、要確認です。
こうした物の寸法は社内標準で決められている事が多いので、
それに従うようにしましょう。
社内標準になければJISに従いましょう。
(JISの参考ページ:http://kikakurui.com/b9/B9713-1-2004-01.html)
具体的な検図の方法
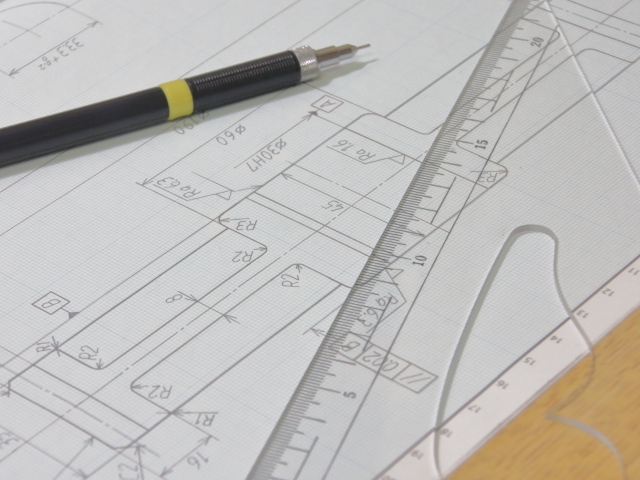
検図に必要な環境
検図の確認ポイントを抑えたところで、ここからは具体的な検図のやり方を紹介します。
効率的に検図を行うためには、以下を意識して環境を整える事が大切です。
- 図面全体が一目で見える事
- コメントや絵を直接記入しやすい事
図面全体が一目で見える事
「パソコンで図面を見ると、どうも頭に入って来にくい」という経験はありませんか?
私は完全にそうです。
原因はおそらく、図面全体が一目で見えない事です。
パソコンの小さい画面で図面の詳細部を拡大して見てると、視野が狭くなり、
図面全体のどこを見てるのか分かり難くなります。
全体が一目で見えた方が拡大縮小の手間が省けて効率的ですし、
「このボルト、なんか位置がずれてて不自然じゃない?」といった、
全体的な違和感にも気付きやすくなります。
コメントや絵を直接記入しやすい事
検図で気付いた内容をチェックバックする際、
文章だけでは図面のどの場所の話をしてるのか分かり難いです。
また修正内容の細かい部分まで文章で伝えようとすると、なかなか大変です。
そんな時「この場所をこんなイメージで修正して欲しい」というコメントや絵を
図面に直接書いて渡せば、意思疎通がスムーズになります。
オススメの検図方法
検図に必要な環境となる
- 図面全体が一目で見える事
- コメントや絵を直接記入しやすい事
の両方を満たすオススメの検図方法はズバリ、
「A3サイズに印刷して手書きコメントし、それをスキャンしてデータで送る」です。
少しアナログな方法ですが、図面はやはり紙に印刷するのが一番頭に入りやすいです。
A3サイズにする理由は、少し大きめの紙に印刷した方が、細かい線も見やすいからです。
また余白も増えるので、メモや修正イメージ図を書きやすくなります。
デジタルな方法に拘ろうと思えば、A3サイズ以上のディスプレイを用意して、
何らかのソフトを使ってメモを追記する事も出来ますが、
私はあまりしっくりきませんでした。
また「修正のイメージ図」の描きやすさは手書きに軍配が上がります。
従って今のところ、私の中で検図方法の最適解は
「A3サイズに印刷して手書きコメントし、それをスキャンしてデータで送る」です。
まとめ
設備設計における検図の確認ポイントと、
具体的な検図の方法を紹介しました。
検図の確認ポイントは、以下の通りです。
- 主仕様に認識違いは無いか
- 主仕様を満たせる機器構成になっているか
- 組立手順はイメージできるか
- ボルト・ナットに手が届くか、工具で回せるか
- 溶接部に手が届くか、無理な体勢にならないか
- 既設範囲と新設範囲の取合いは明記されているか
- 相手側の位置が予想と少しずれていた場合、調整代はあるか
- 周りの物と干渉しないか
- 主要部材の強度は十分か
- 自重や外荷重を受ける箇所の強度は十分か
- 高頻度で交換する部品、消耗品が取外し難くなっていないか
- 日常点検が必要な部品が見えない位置にいないか
- 可動する物がある場合、身体が挟まれないか
- 回転体が露出しており、巻き込まれないか
- 高温物が露出しており、火傷しないか
- 階段や通路の位置、手摺の高さは適切か
どんな設備を設計しているかによって確認ポイントは変わってきますが、
上記を抑えておけばとりあえず致命傷は避けられます。
また検図を行う環境としては、以下の2つのポイントが大切です。
- 図面全体が一目で見える事
- コメントや絵を直接記入しやすい事
これらを満たし効率的に検図を行える最適解は
「A3サイズに印刷して手書きコメントし、それをスキャンしてデータで送る」です。
いかがだっだでしょうか。
今回の記事が皆さんの参考になれば幸いです。